Lamination control
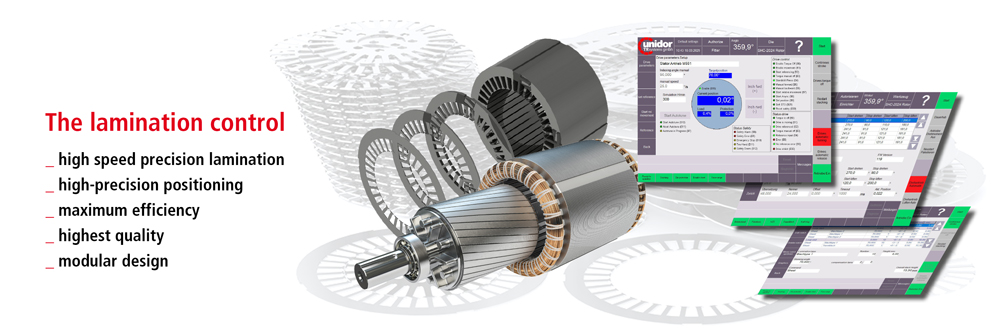
Lamination control with compactPRESS
Highly dynamic servo rotary motors
Selection of highly dynamic servomotors with various torques, also with water cooling if required. Assistance with motor design based on mathematical models by our support team. Very high positioning accuracy.
Scalable and customizable system
Up to 12 independent packaging channels / products. Independent control of up to six rotary motors, which can be can be flexibly assigned to the packaging channels. Up to 16 sliders incl. end position monitoring per packaging channel. Inputs and outputs can be assigned flexibly & depending on the tool.
Expandable system
Comprehensive integration of necessary peripherals for rotor/stator rotor/stator production such as package post-processing (e.g. presses / package height measurement). Strip thickness measuring systems gluing systems Integration of feed systems (push/pull & waste shears) from different manufacturers Flexible expansion with process monitoring functions such as press force measurement (to detect punch breakage etc.); double sheet measurement; etc. Extension with data acquisition and Industry 4.0 OPC UA interface and much more.
compactPRESS industrial PC
Intuitive, customizable touch HMI according to industry standard Extensive tool safety functions User-friendly interface EtherCAT fieldbus with <=100μs cycle time
The lamination control (SHC) takes over the complete control and monitoring of the punch pack process
- Measurement of the strip thickness (multi-channel)
- Multi-track operation
- Multi-channel pack counter
- Snap-in programming with sheet counting or at pack height
- Loop programming
- Multiple sliders per channel with freely selectable slider position
- Angle range or switchover point programmable for each pusher
- Laser stacking or pusher is available for several strokes
- End position monitoring with 2 inputs per slider
- Invert slider output
- Copying of packaging channels in the tool
- Document package height (AMT channel)
- Static/dynamic ejection monitoring
- Conveyor belt monitoring
- Turning (restacking) and twisting
- Lifter and pusher control
- Feed control (pulling/pushing)
- Programmable scrap shear control
- Process monitoring (punch waste, punch breakage, etc.)
- Integration of various peripheral devices possible
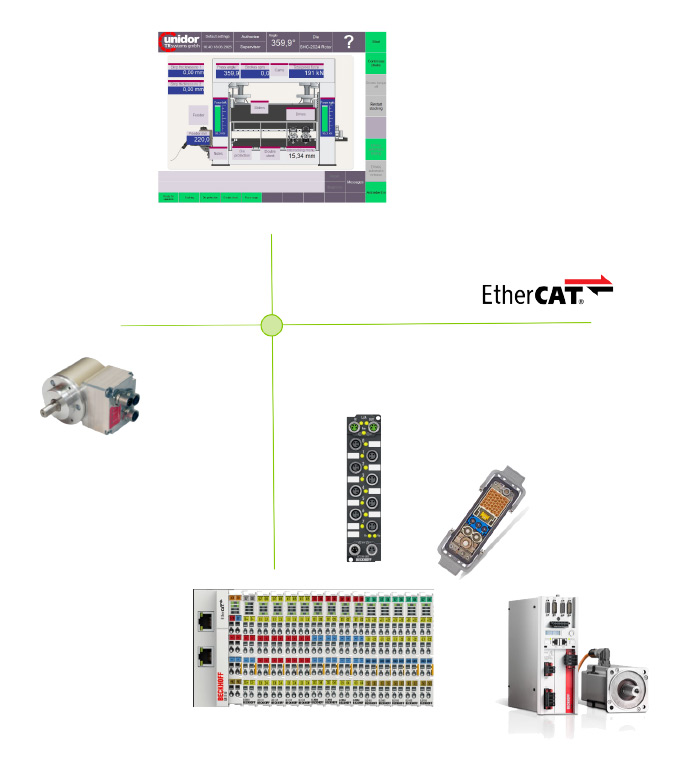
Functions
Strip thickness measurement
All sensors with an output voltage of -10 V..+10 V can be connected. The sensor linkage (e.g. differential measurement) can be internal or external. The sensor characteristic can be linearized and offset-calibrated with several interpolation points.
Insert strip
After starting the function, a programmable number of separator plates are produced. Duration: Distance between infeed and lamination point.
Ejection monitoring
Ejection monitoring can be static or dynamic. Static: The status of the sensor must not change for n strokes. Dynamic: at least one change must take place aftern strokes.
Conveyor belt monitoring
The conveyor belt must emit m pulses in n strokes. The conveyor belt is switched off when the machine is at a standstill with programmable overrun. Start with “clutch on”.
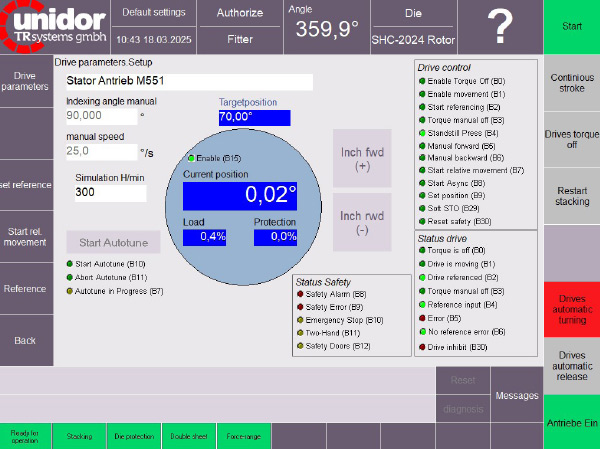
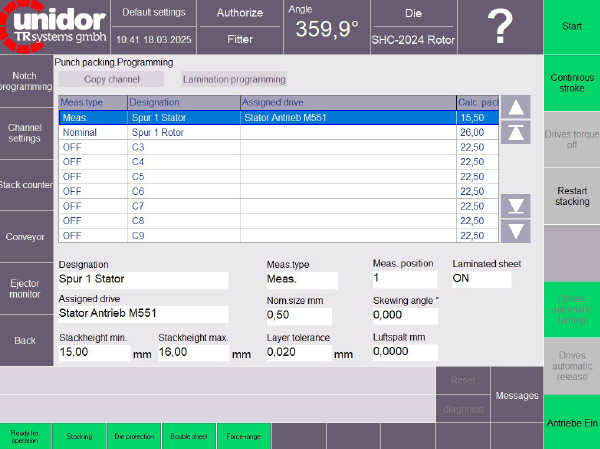
Prospect